Introduction
Clean water is an extremely valuable resource whose availability is becoming increasingly scarce worldwide. It is therefore essential in the long term to take measures to use water as sparingly and efficiently as possible. One promising solution in this context is the Zero Liquid Discharge (ZLD) process.
Zero Liquid Discharge is an innovative concept that aims to recycle and reuse all wastewater from industrial processes instead of discharging it into the environment. It involves a complex system of different water treatment technologies that ensure that virtually no liquid waste is discharged into the wastewater system.
The aim is not to release any liquid waste into the environment. Wastewater treatment always leaves a residue of highly concentrated waste, but this residue can either be recycled or disposed of properly.
Since in both cases "zero" liquids are "discharged" into the "environment", the term "zero liquid discharge" can be justified as "zero waste in the environment".
What is Zero Liquid Discharge?
Zero Liquid Discharge is a process for industrial wastewater treatment that aims to treat and purify all wastewater within the company's own production facilities and reintegrate it into the production cycle as far as possible.
The disposal of contaminated process water is cost-intensive, which is why ZLD also generates a major economic advantage in the long term, as the acquisition costs (e.g. of a vacuum distillation system) are amortized in just a few years.
Basic principles of ZLD
ZLD systems consist of several treatment steps that are specially designed to clean and concentrate the wastewater in different ways:
Chemical and physical pre-treatment
In this step, coarse impurities are removed and the water is prepared for the subsequent treatment phases. Processes such as flocculation, sedimentation and filtration are used here.
Membrane Filtration
Technologies such as ultrafiltration and reverse osmosis are used to remove dissolved solids and impurities from the water. This significantly reduces the level of contamination in the residual water to be treated.
Thermal treatment
The water is further concentrated using evaporation technologies. The water is heated and evaporated, leaving behind the contaminants as a concentrated residue. In general, only 2% of most industrial wastewater or process water consists of contaminants. Vacuum evaporation technology therefore makes a huge contribution to drastically reducing the disposal volume.
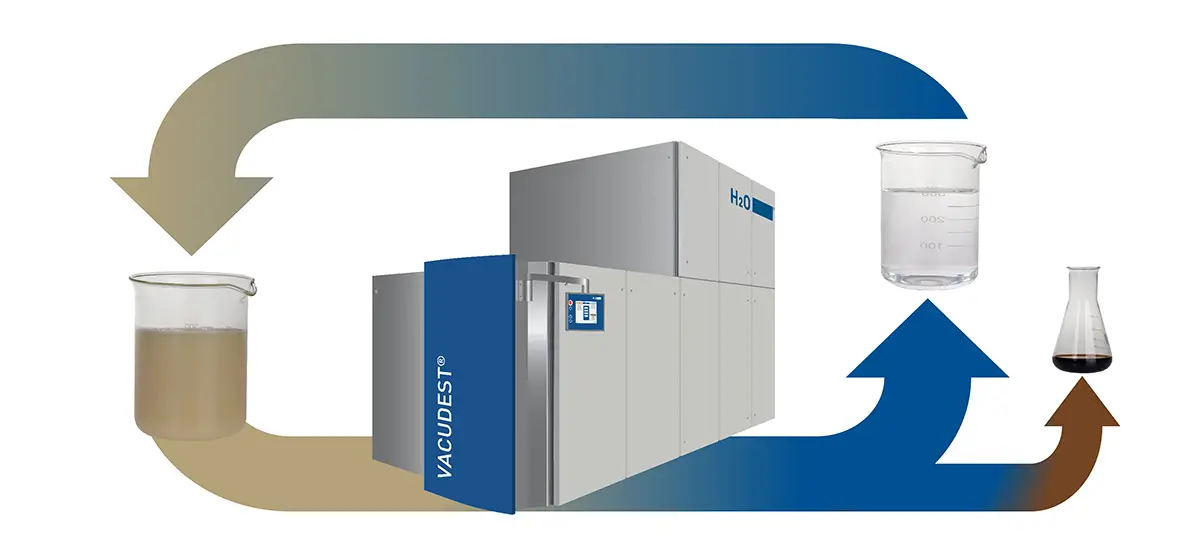
Comparison of the Zero Liquid Discharge process with the disposal of wastewater or process water
Many companies still rely on traditional methods of wastewater disposal, where all contaminated water is disposed of. This practice is not only expensive, as high disposal fees are incurred depending on the volume to be disposed of (or how problematic the wastewater is), but also inefficient, as valuable resources are wasted.
In contrast, ZLD offers numerous advantages. It reduces the amount of waste water that needs to be disposed of to a minimum. It also enables the reuse of purified water in the company's own industrial processes. This leads to significant cost savings and easier compliance with environmental regulations. Another important aspect of ZLD is its independence from external water sources, which is particularly advantageous in regions with water shortages.
Good reasons for the introduction of Zero Liquid Discharge processes
The introduction of Zero Liquid Discharge in industrial processes offers numerous advantages, both environmental and economic. The main reasons for implementing ZLD are as follows:
Compliance with legal regulations and environmental requirements
In many countries, the requirements for wastewater disposal are constantly increasing. Stricter environmental regulations and discharge limits make it necessary for companies to optimize their wastewater treatment processes. With ZLD, companies can ensure that they comply with these requirements and avoid potential penalties or sanctions. This is particularly relevant in regions with strict environmental regulations, such as the USA or the EU.
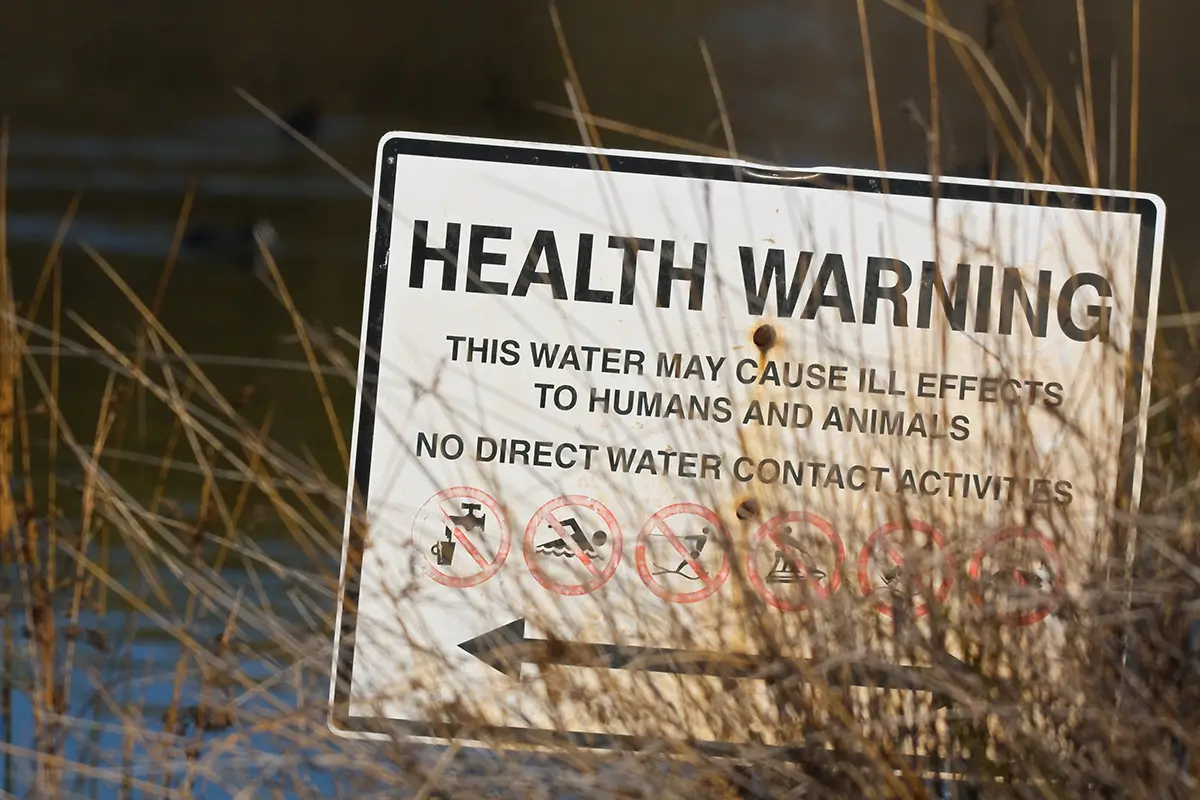
Economic benefits and cost efficiency
The disposal of wastewater can be very costly for companies. Traditional methods of wastewater treatment require high operating costs and continuous investment in infrastructure to meet regulatory requirements. ZLD systems allow companies to reduce these costs by reusing the treated water, minimizing the amount of wastewater that needs to be disposed of. In the long term, this leads to significant savings and improved profitability.
Comparison to disposal of industrial wastewater
Sustainability and conservation of water resources
Clean water is an increasingly scarce resource. There is already a water shortage in many regions of the world and the demand for clean water is constantly increasing. This is not only the case in third world and emerging countries, but now also in highly developed industrialized nations such as the USA. Here, highly populated states such as California suffer greatly from water shortages.
Please also note the information provided by the European Commission: Water Scarcity and Droughts
By introducing ZLD, companies can significantly reduce their water consumption and make an important contribution to the sustainable use of water resources. This is not only beneficial from an environmental point of view, but also improves the company's public image as a responsible and environmentally friendly player.
Independence from fresh water sources
The availability of fresh water can be unreliable in many regions. Natural disasters, droughts and other environmental factors can affect water supplies. With ZLD systems, companies can reduce their dependence on external sources of fresh water and ensure that they can maintain their production processes even in times of water scarcity. This increases operational security and resilience.
Reuse and recycling of waste materials
Another advantage of ZLD is the possibility of recycling concentrated waste materials. In some cases, the residues from ZLD processes can be used as raw materials in other industrial applications, such as fuel or the reuse of salts in hardening shops. This contributes to the circular economy and reduces the amount of waste that needs to be disposed of. In some industrial sectors, such as the electrical, electroplating and jewelry industries, ZLD can be used to recover valuable metals such as palladium, silver, gold or platinum, as these are used in these industries for processing or coating, as catalysts or in components, for example.
Read our case study on Montblanc writing instruments here: Saving on electroplating costs
Positive perception and competitiveness
The implementation of ZLD can significantly improve a company's image. Customers and business partners appreciate environmentally conscious and sustainable practices. A positive public image can help to increase the company's competitiveness and open up new business opportunities. In addition, companies that adopt ZLD can position themselves as pioneers in their industry and potentially benefit from funding programs and government incentives.
Technologies and processes in ZLD plants
1. Pre-treatment and pre-concentration
In the case of coarse impurities, pre-treatment must take place before any other treatment phase in order to eliminate solids. Various physical and chemical processes are used here, such as:
Sedimentation: "settling" of solids by gravity (e.g. sand, soil, glass or metal splinters)
Flocculation and precipitation: use of chemicals to bind and separate particles
Filtration: Use of media and belt filters to remove fine particles and suspended matter.
2. Waste water treatment
Membrane process
After pre-treatment, the water is further purified using membrane processes. These technologies are particularly effective at removing dissolved substances and very fine particles:
Ultrafiltration (UF): Removes colloids, macromolecules and bacteria
Reverse osmosis (RO): Removes dissolved salts, organic compounds and other impurities.
Thermal processes
Thermal processes play the central role in the ZLD process, as they separate clean water through evaporation, leaving behind a significantly reduced volume (up to 98% reduction) of wastewater. The most important thermal technologies include
Vacuum evaporator: The evaporation process takes place under reduced pressure. As a result, the process water evaporates at much lower temperatures than without the generation of a vacuum. As the process water, depending on the strength of the vacuum, evaporates at around 85 degrees Celsius instead of 100 degrees Celsius (at atmospheric pressure), a lot of energy can be saved. Vacuum evaporators often use a mechanical vapor compressor to compress the vapor produced during distillation. This compressed vapor is then fed back to the outside of the heat exchanger, allowing the heat from the vapor to be reused. This further increases energy efficiency.
Low-temperature evaporator: With this type of evaporator, the wastewater is evaporated to < 50 °C at negative pressure using a heat pump. The type of heat pump evaporator, e.g. air-to-water evaporator, water-to-water evaporator and brine-to-water evaporator, has just as great an influence on the investment costs (earthworks and drilling required in some cases) as the climatic conditions.
3. Final concentration and crystallization
In a final optional phase of the ZLD process, the remaining residual water is further evaporated until only relatively viscous or crystalline residues remain. This post-concentration is often very energy-intensive due to high intermolecular interactions. Post-concentrators that utilize the energy from the upstream wastewater treatment have advantages in terms of energy consumption. These require up to 85% less energy than conventional post-concentrators. VACUDEST ZLD 300
These residues can then either be disposed of safely or recycled. Crystallizers in particular are used here to crystallize and separate the solids.
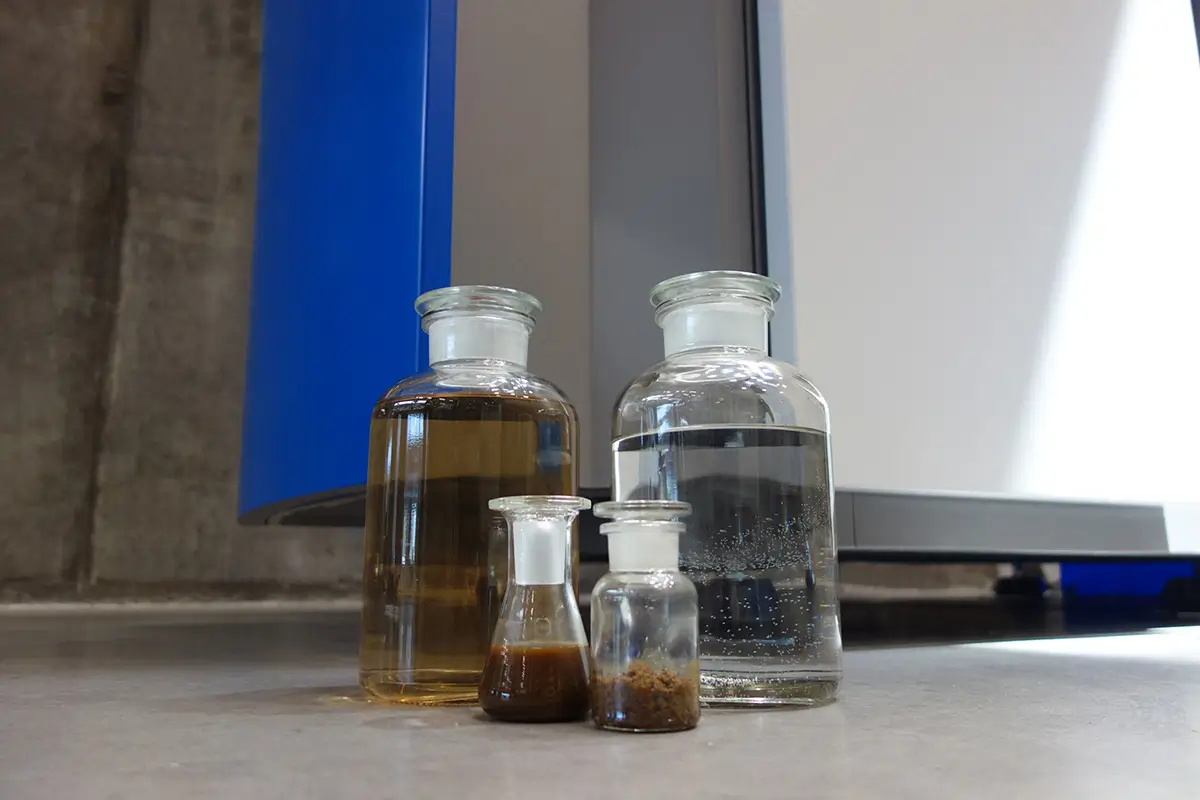
Reuse and recycling
The treated water and solid residues from the ZLD process can be reused in various industrial applications. For example, purified water can be used for cooling processes or as process water, while the solid residues can in some cases be reused as a raw material for other processes, such as the recovery of precious metals in the jewelry and watch industry.
The combination of these technologies and processes enables ZLD plants to treat wastewater efficiently and recycle it almost completely.
Case studies for application in the industry
Zero Liquid Discharge is used in a wide range of industries, all of which benefit from the unique advantages of this technology. Some of the most prominent users include the automotive, aerospace, chemical, pharmaceutical, metalworking and electronics industries. Each of these industries has specific wastewater treatment requirements that can be met by ZLD solutions. It should also be noted that in the chemical and pharmaceutical industries, the residues cannot be reused and must be disposed of.
Case study: Swiss company for concrete admixtures and sealants
SIKA AG in Gournay-en-Bray, France, produces its products in large vats in which the reagents are mixed. Before the vats are transferred to the next production stage, they have to be cleaned with water. The used and contaminated water is then stored in large containers until it is treated. The wash water contains impurities such as hydrocarbons, salts and surfactants.
By using a VACUDEST 4.500 Clearcat from H2O, SIKA AG avoids having to send its wastewater to the municipal sewage treatment plant and at the same time frees itself from the need for regular wastewater inspections by the local authorities. SIKA AG also decided to use this system because of its simple automated operation and low-resource maintenance.
Freedom from wastewater-related restrictions: SIKA installs a Clearcat vacuum distillation system
Other industrial applications
ZLD technologies are also used in the electronics industry, where they help to ensure high-purity water qualities for production. In metalworking and metal processing, ZLD helps to treat and reuse oily wastewater. In the chemical and pharmaceutical industries, ZLD enables the treatment of complex wastewater streams. In the jewelry and watchmaking industry, for example, even the precious metals from the residue can be reused, as can the salts in the hardening shop.
Advantages and successes
The implementation of ZLD in various industries has shown that this technology not only significantly reduces environmental impact, but also lowers operating costs and increases resource efficiency.
Case Studies
Sony DADC
For a modern, sustainable company like Sony DADC, wastewater-free production was one of the most important requirements. The new ZLD system now runs automatically and is available around the clock without a great deal of supervision, which is a decisive advantage over the chemical-physical wastewater treatment that was previously used.
Sony DADC Austria in Thalgau expands production and becomes wastewater-free
SEW Eurodrive
What should a ZLD system be able to do? For SEW, this was clear: it must achieve a high treatment quality for demanding processes, be space-saving and have good customer service. For this project, wastewater streams from die casting and cooling lubricants were combined and treated together. This enabled SEW USOCOME's production to be made wastewater-free and the treated water to be reused in the production process.
AUDI AG
Audi realized a ZLD system based on the VACUDEST S 600 in order to be able to include the factors of process reliability and sustainability in addition to efficiency in terms of operating costs. The aim was to create a simple, uncomplicated system that would not distract from the main task of production in the foundry.
Sustainable processing of foundry wastewater at AUDI AG on the site in Münchsmünster
ZINKPOWER – HEAD GRUPPE
Sustainable and economical production - this was also the wish of the company ZINKPOWER Coating Schopsdorf in Saxony-Anhalt. They opted for a ZLD system with a size L VACUDEST vacuum distillation system with Clearcat. The rinsing water treated in this way and post-treated with an ion exchanger is ideal for reuse in the powder coating of components made of steel, hot-dip galvanized steel and aluminium.
Efficient rinsing water treatment with VACUDEST enables circulation at Zinkpower
Economic efficiency and operating costs
The cost-effectiveness of Zero Liquid Discharge systems depends on various factors, including initial investment costs, ongoing operating costs and long-term savings. Although the implementation of ZLD technologies is associated with (relatively) high initial investments, they offer significant economic benefits in the long term.
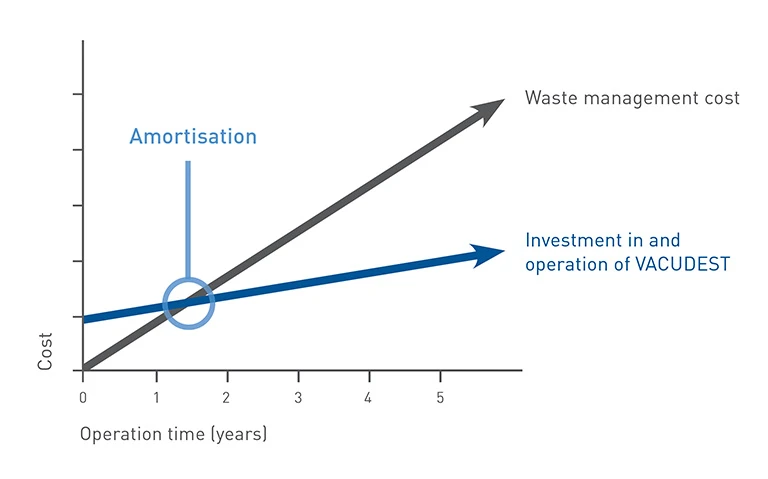
Technological support and advice
The successful implementation of Zero Liquid Discharge systems requires specialized technological support and sound advice. Companies wishing to introduce ZLD can benefit from the expertise and services of specialized providers who offer customized solutions and comprehensive support.
Advice and planning
Planning and implementing a ZLD system begins with a detailed analysis of the company's specific requirements and conditions. Specialized consultants Specialized consultants help to select the best technologies and processes that meet the individual needs and objectives of companies. This includes the selection of suitable technologies based on laboratory tests of the wastewater sample. Based on the results, the most suitable pre-treatment processes, membrane and thermal technologies, possible post-treatment methods and the integration of these systems into the existing infrastructure are also presented and recommended, in addition to the selection of the right vacuum distillation system.
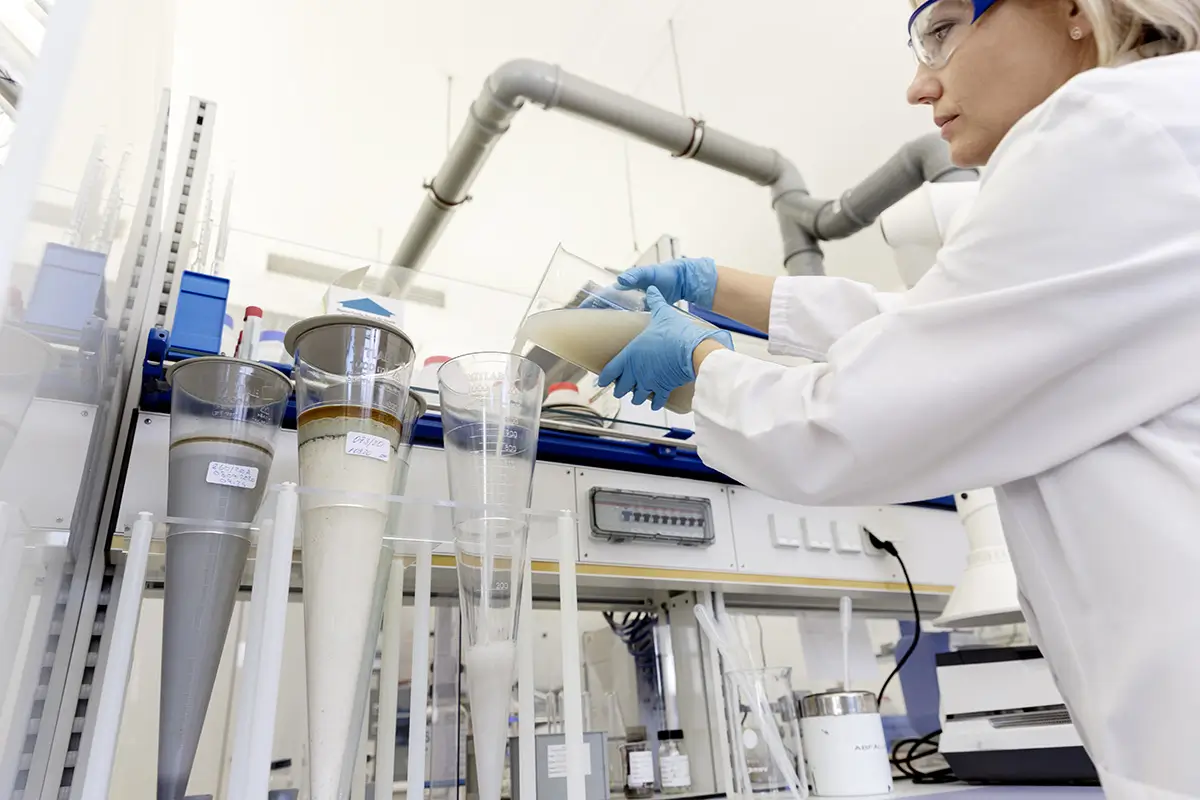
Technological solutions
Leading suppliers such as H2O GmbH offer innovative, technological solutions that are tailored to the needs of various industries. They specialize in vacuum evaporation systems, which have proven to be the best and most sustainable treatment method in many industrial sectors.
The company also develops unique technologies that improve the treatment quality depending on the industrial wastewater and requirements, thus enabling reuse in its own production. These include the minimization of oils (link to Clearcat), the reduction of COD (link to Purecat), the maintenance of a constant pH value (link to Destcontrol) or specialized post-concentrators that ensure the implementation of ZLD with maximum efficiency and reliability thanks to energy recycling.
Training and maintenance
In addition to providing the technology, specialist providers also offer comprehensive training programs for operating personnel. These training courses ensure that employees can operate the ZLD systems efficiently and safely and that potential sources of error and incorrect operation are eliminated as far as possible. In addition, many providers offer maintenance and support services to ensure the long-term operation and performance of the systems. Regular inspections, preventive maintenance and technical support are crucial to ensure that the systems function optimally.
There are also already smart wastewater systems that use digital analyses and recommended actions to increase the efficiency of the ZLD system and thus increase system availability.
Innovations in smart wastewater systems
Subsidies and financing
Companies can also benefit from government funding programs and financial incentives that support the implementation of ZLD technologies. Specialized consultants can help identify suitable funding opportunities and support the application process to reduce financial investment and facilitate the transition to greener practices.
Commissioning and operation of ZLD systems
The commissioning and operation of Zero Liquid Discharge systems requires careful planning and continuous monitoring to ensure optimal results. Companies need to consider various aspects to maximize the efficiency and reliability of their ZLD systems.
Important steps for commissioning
The successful launch of a ZLD system begins with a detailed preparation phase. This includes the selection of suitable locations, the integration of the plant into the existing infrastructure and the training of operating personnel. Before commissioning, all components of the ZLD plant must be thoroughly tested to ensure that they function properly and achieve the desired wastewater treatment objectives. An important step in this process is the fine-tuning of the various treatment stages to ensure maximum efficiency and water purification .
You can find a detailed article on setting up a vacuum distillation system here
Operation and maintenance
The continuous operation of a ZLD system requires regular maintenance and monitoring. It is crucial that operating personnel are regularly trained and informed about the latest procedures and technologies. Maintenance activities include inspection and cleaning of membranes, evaporators and other key components to minimize scaling and wear. Regular inspections of the process are useful to ensure that the plant maintains consistently high cleaning standards. This can also be carried out remotely at low cost, for example. Remote maintenance involves experts connecting to the system to provide efficient and fast assistance.
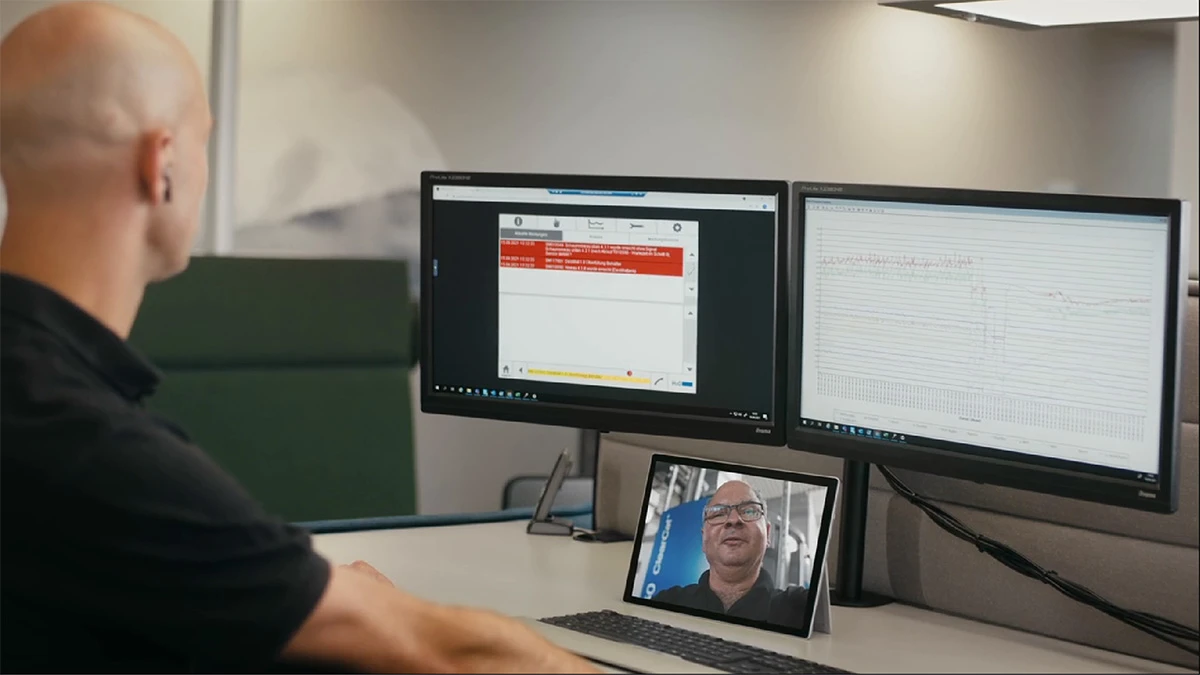
Optimization and adaptation
During operation, it is important to continuously monitor the performance of the ZLD system and make adjustments to increase efficiency. This can include adjusting chemical dosages of operating fluids, optimizing operating temperatures and monitoring energy consumption. Modern plants are often equipped with advanced control systems that enable preventive maintenance through real-time monitoring and adjustment to optimize operations and reduce operating costs.
Innovations in smart wastewater systems
Future prospects and innovations in the ZLD sector
Technologies used in the Zero Liquid Discharge process are constantly evolving to meet the increasing demands on environmental standards and resource management. Innovations in this area are aimed at further improving the efficiency and cost-effectiveness of ZLD systems and opening up new application possibilities.
Current developments and trends
One of the most significant developments in the field of ZLD is the improvement of the energy efficiency of evaporation technologies. Modern evaporators use advanced heat recovery systems that significantly reduce energy consumption. The use of renewable energies to supply energy to ZLD systems is also becoming increasingly important, which further improves the environmental footprint of these systems.
Integration of membrane technologies
Membrane technologies, such as nanofiltration and reverse osmosis, offer improved options for the treatment and concentration of wastewater. These technologies are particularly effective in removing dissolved substances and help to increase the efficiency of the overall ZLD processes. The integration of such membrane systems makes it possible to lower energy requirements and reduce operating costs.
Automation and digitalization
The automation and digitalization of ZLD systems are other important trends. Modern control and monitoring systems enable real-time monitoring of system performance and automatic adjustment of operating parameters. This leads to optimized operational management and minimizes the risk of downtime. In addition, data-based analyses can help to continuously improve the efficiency of the systems and identify potential problems at an early stage.
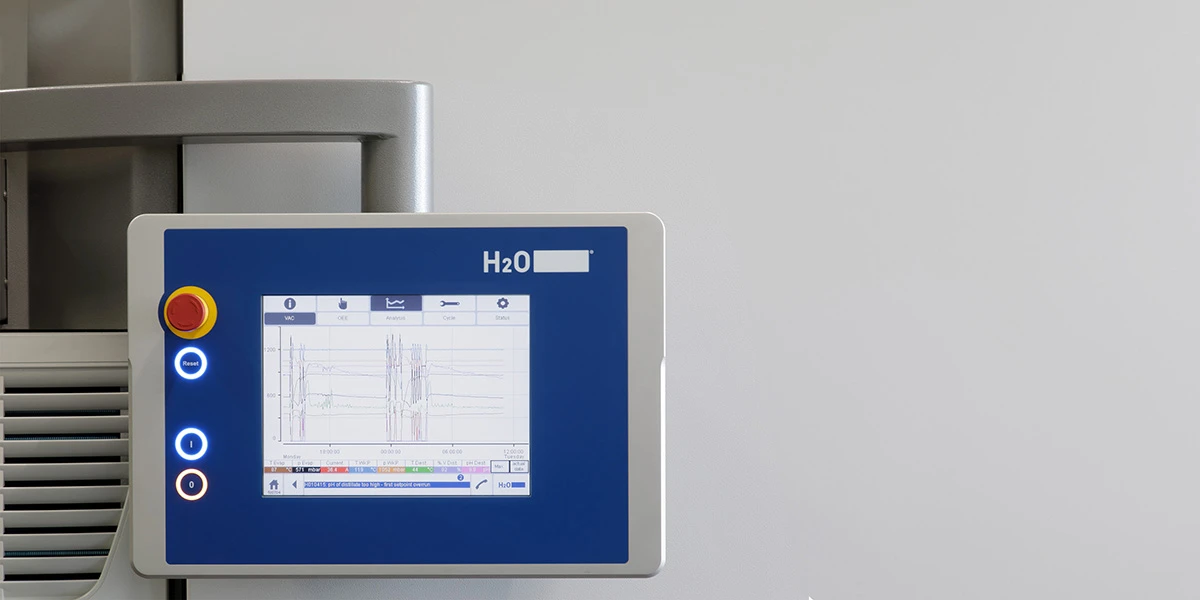
Extended application areas
ZLD technologies are increasingly being used in new industrial sectors that were previously not in focus. These include, for example, the food and beverage industry and the textile industry, which can benefit from this technology due to its high water consumption and strict environmental regulations.
Research and development projects
There are numerous ongoing research and development projects aimed at further optimizing Zero Liquid Discharge technology. These projects focus on the development of new materials and processes to improve the efficiency of water treatment and reduce costs.
Some companies have an interdisciplinary team of experts who are continuously working on the development of advanced solutions for a wastewater-free factory. In recent years, for example, H2O GmbH has been able to present pioneering innovations that have enabled numerous and diverse industrial companies to achieve wastewater-free production. These include post-concentrators and technologies to improve distillate quality, such as the Clearcat condensation stage. As an integrated module based on physical and catalytic effects, the Clearcat enables virtually oil-free distillate in just a single process step and requires neither energy nor auxiliary or operating materials. Requirements for reuse are thus met both qualitatively and economically.
The benefit of this technology is the elimination of multi-stage, complex processes for the reduction of oils and fats in wastewater. These are usually necessary in order to reduce the oil index in the process water to such an extent that the treated water can be reused. Although companies can also develop pioneering innovations on their own, cooperation between research institutions, industry and government is crucial for the future in order to promote innovative solutions and accelerate their market maturity.
Summary and conclusion
Zero Liquid Discharge offers companies significant environmental and economic benefits that outweigh the effort and initial costs in the long term. By almost completely recycling and reusing wastewater, companies can save costs, comply with legal requirements and minimize their environmental impact.
The three most important factors are the technology:
- Resource efficiency: ZLD systems enable the almost complete reuse of water, which reduces dependence on external water sources and lowers the cost of fresh water. This is particularly advantageous in regions where water is already in short supply.
- Sustainability and public image: By minimizing the discharge of wastewater into the public sewage system and disposing of only minimal residues after water treatment, ZLD makes a significant contribution to the company's environmental friendliness. This enables them to achieve their sustainability goals and present themselves positively in the eyes of the public.
- Cost-effectiveness: Despite relatively high initial investments, ZLD systems usually pay for themselves within a few years thanks to savings in disposal and operating costs. Ongoing process optimization and automation also contribute to high cost efficiency.
For companies considering making their production wastewater-free in the future, H2O GmbH offers comprehensive solutions and years of expertise in the field of ZLD. With innovative technologies such as the Clearcat condensation stage and vacuum distillation systems adapted to the process water, H2O supports companies in making their wastewater treatment efficient and sustainable. Thanks to successful implementations in various industries, H2O is a reliable partner for the realization of wastewater-free production processes.